ATEMAG Control 4.0 retrofitting
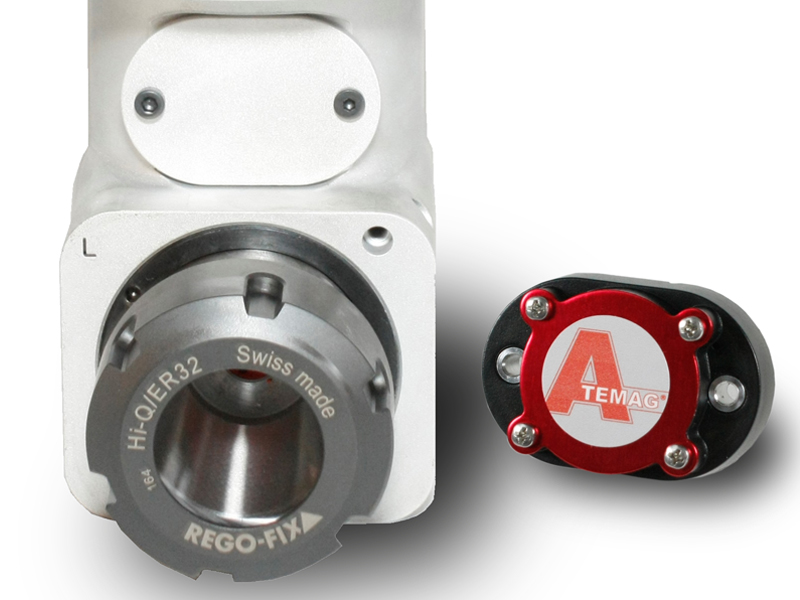
Retrofitting of the high-tech Control 4.0
Retrofitting the Control 4.0 chip on your ATEMAG aggregate is simple and cost-effective.
Above all, you benefit by:
- Increasing the performance of your aggregate
- Optimized service interval
- Integrated wear control
- Remote maintenance
The retrofit is that simple:
- Send us the serial number of your aggregate with the order of an ATEMAG Control 4.0 Chip
- We will set up your Control 4.0 chip and send it directly to you
- You simply mount your new Control 4.0 chip on your aggregate
- Finally, log in to the cloud and register.
______________________________________
The Control 4.0 chip is attached directly to your aggregate and provides constant, near real-time data via a data stick using Bluetooth and WiFi.
The high-tech sensors of the ATEMAG Control 4.0 chip can record precise data of the aggregate. Based on this data, the machine operator can recognize whether critical parameters have been reached and settings on the machine should be changed or if the aggregate should be serviced.
The ATEMAG Control 4.0 technology determines the following performance data during the processing times:
- rotation speed (rpm)
- working hours
- temperature
- vibration
The ATEMAG Control 4.0 chip communicates constantly with the aggregate and records load fluctuations. These are constantly transmitted to the cloud in near real time via a data stick using Bluetooth and WLAN. Based on that data, the machine operator can intervene in the process if necessary.
Based on the data transmitted by the Control 4.0 chip, which can be viewed by the machine operator at any time, the aggregate can be accessed individually to change parameters for process optimization. This targeted modification of the operating parameters allows the aggregate to be brought to maximum performance in a controlled manner, which in turn is beneficial for the optimization of the production capacity.
The operating hours counter integrated in the Control 4.0 chip reports all service intervals recommended by ATEMAG.
This allows the machine operator to plan the timely maintenance of the aggregate, thus avoiding unwanted downtime. This way the implementation of a precise, smooth and cost-effective maintenance plan can be ensured.
The sensors of the ATEMAG Control 4.0 chip permanently monitor the performance data of the aggregate in near real time. The data collected in the chip is analyzed and transmitted to the Cloud. If critical parameters are exceeded, the Control 4.0 technology communicates directly with the machine operator and points out malfunctions. The machine operator can then take corrective action by changing the parameters. This prevents unwanted damage to the aggregate.
Thanks to the implemented cloud of the Control 4.0 chip, each aggregate can be monitored anywhere in the world at the customer's request.
Analysis test runs are then used to determine the status of the aggregate to be monitored.
Based on the data obtained during remote maintenance, the customer is then informed when maintenance is recommended.
In addition, the customer can be brought attention to about load fluctuations so that he can change the operating parameters in time to achieve maximum performance
Explanatory video of theControll 4.0 technology
______________________________________
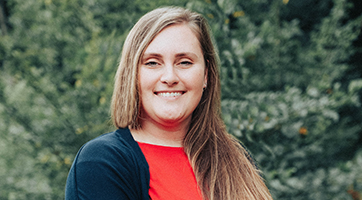
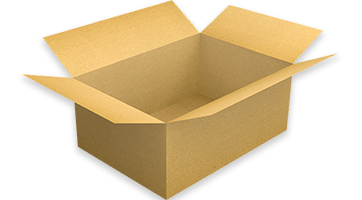
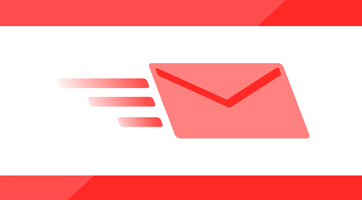